I. Introduction
Cost management is a critical aspect of running a successful business. In order to thrive in today’s competitive market, organizations must have a clear understanding of their costs and how they affect their overall profitability. One approach that has gained significant popularity in recent years is Activity-Based Costing (ABC). This strategic cost management method provides a more accurate and detailed picture of a company’s costs by tracing them back to specific activities within the organization. In this article, we will delve into the world of ABC, explore its benefits, and analyze its applications across various industries.
II. Traditional Costing Methods
Before diving into ABC, it is essential to explore the traditional costing methods that have been widely used in business for decades. Traditional costing methods such as job order costing and process costing have proven to be effective in certain scenarios. However, they come with limitations and challenges that often lead to inaccurate cost allocation. Factors like arbitrary cost allocations, inappropriate overhead calculations, and the difficulty in differentiating between indirect and direct expenses can distort cost information.
III. Understanding Activity-Based Costing (ABC)
Activity-Based Costing (ABC) is a modern cost management technique that aims to address the limitations of traditional costing methods. ABC takes a more granular approach by focusing on the activities performed within an organization and linking them directly to the costs they generate. By analyzing the activities that consume resources, ABC provides a clearer understanding of how costs are incurred throughout the organization.
Benefits and advantages of ABC
Implementing Activity-Based Costing brings several benefits to organizations. One advantage is the ability to allocate costs more accurately, resulting in a better understanding of individual product and service profitability. By uncovering previously obscured costs, ABC enables companies to make more informed decisions regarding pricing, resource allocation, and product development.
IV. Key Concepts of Activity-Based Costing
To implement ABC successfully, it is vital to understand its core concepts. The following key concepts form the foundation of Activity-Based Costing:
1. Identifying cost drivers and activities
Cost drivers are the specific factors that cause costs to be incurred within an organization. Activities, on the other hand, are the tasks and processes performed to deliver products or services. ABC focuses on identifying the activities that drive costs and determining the cost drivers associated with each activity.
2. Allocating costs based on activities
Once cost drivers and activities are identified, ABC allocates costs based on the consumption of resources by each activity. This allows for a more accurate determination of the true cost of each product or service offered by the organization.
3. Activity-Based Costing formula and calculations
The calculation of costs under ABC involves assigning overhead expenses to activities and then allocating those costs to products or services. The formula used in ABC calculations is:
Cost per Activity = Total Activity Cost / Total Activity Driver Quantity
By using this formula, organizations can better understand how costs are distributed based on the usage of resources.
V. Implementing Activity-Based Costing
Implementing ABC requires careful planning and execution. Here are the steps involved in transitioning from traditional costing to Activity-Based Costing:
1. Identify activities and cost drivers
The first step in ABC implementation is to identify the specific activities performed within the organization. Additionally, the cost drivers associated with each activity need to be determined. This involves a detailed analysis of the operations, processes, and resource consumption throughout the organization.
2. Assign costs to activities
Once the activities and cost drivers are identified, it is necessary to assign costs to each activity. This involves analyzing the overhead expenses and labor costs associated with each activity and allocating them accordingly.
3. Allocate activity costs to products or services
After assigning costs to activities, the next step is to allocate those costs to individual products or services. This allows for a precise understanding of the cost incurred by each offering.
4. Test and refine the ABC system
Implementing ABC is an iterative process that requires continuous monitoring and refinement. It is crucial to test the system, analyze the results, and make necessary adjustments to ensure accuracy and reliability.
VI. Industries and Applications of Activity-Based Costing
While ABC can be applied to various industries, it has gained significant traction in manufacturing, the service industry, and healthcare organizations.
1. Activity-Based Costing in manufacturing
Manufacturing companies often have complex operations with multiple cost drivers and activities. Implementing ABC in this sector provides insights into the true costs associated with each product, enabling companies to optimize their production processes, streamline resource allocation, and make well-informed pricing decisions.
2. ABC in the service industry
The service industry, which includes sectors such as banking, insurance, and consulting, can also benefit from ABC. This method helps service providers identify the activities that consume resources and allocate costs more accurately. By understanding their cost structure, service organizations can optimize their offerings, improve customer satisfaction, and enhance profitability.
3. ABC and healthcare organizations
Activity-Based Costing has proven to be particularly valuable in healthcare organizations. With complex healthcare delivery systems and a multitude of cost drivers, ABC enables hospitals and healthcare providers to analyze the true costs of patient care, optimize resource allocation, and make more informed decisions in the face of limited resources.
4. Other industries leveraging ABC
While manufacturing, the service industry, and healthcare are prominent examples, ABC can be applied to almost any industry. Aviation, telecommunications, technology, and even non-profit organizations can benefit from the insights and accuracy provided by ABC.
VII. Limitations and Criticisms of Activity-Based Costing
While Activity-Based Costing brings numerous benefits, it is important to acknowledge its limitations and criticisms. Some common challenges include:
1. Time and resource-intensive implementation
Implementing ABC can be a time-consuming and resource-intensive process. It requires a significant amount of data collection, analysis, and collaboration among various departments. Additionally, training employees to understand and embrace ABC may require substantial effort.
2. Subjectivity in cost driver identification
The identification and selection of cost drivers can be challenging. Different individuals may have varying opinions on which cost drivers are the most relevant, resulting in subjectivity and potential discrepancies in cost allocation.
VIII. Activity-Based Costing vs. Other Costing Methods
It is essential to understand how ABC differs from other costing methods. Let’s compare it to traditional costing and two commonly used alternatives:
1. Comparing ABC with traditional costing
Traditional costing methods typically rely on broad and arbitrary allocations of overhead costs. ABC, on the other hand, traces costs back to the activities that drive them, providing a more accurate picture of cost allocation and enabling better decision-making.
2. Differences between ABC and variable costing
Variable costing only considers direct costs when determining product costs. ABC, however, accounts for both direct and indirect costs, providing a more comprehensive view of cost allocation and profitability.
3. ABC vs. absorption costing
Absorption costing allocates fixed overhead costs to products or services based on predetermined rates. ABC, on the other hand, calculates costs based on actual resource consumption, providing a more accurate understanding of the costs associated with each activity.
IX. Activity-Based Costing and Resource Allocation
One of the significant advantages of ABC is its ability to optimize resource allocation. By linking resource consumption to costs, organizations can identify activities that have a high resource demand and allocate resources accordingly. This ensures that resources are allocated efficiently and only to activities that contribute to maximizing profitability.
X. Activity-Based Costing and Decision-Making
ABC plays a crucial role in enhancing decision-making processes within organizations. By providing accurate and detailed cost information, ABC enables management to make informed decisions regarding pricing, product development, resource allocation, and strategic planning. It helps identify cost-saving opportunities, prioritize investments, and align operations with the overall organizational goals.
XI. Activity-Based Costing and Performance Measurement
Activity-Based Costing can also be utilized as a performance measurement tool. By analyzing key performance indicators (KPIs) derived from ABC data, organizations can evaluate the efficiency and productivity of various activities. This allows for performance comparisons between different departments, products, or services, helping management identify areas for improvement and make informed decisions to enhance overall performance.
XII. Activity-Based Costing for New Product Development
When developing new products, ABC can play a vital role in product costing. By analyzing the costs associated with each product development activity, organizations can accurately determine the costs involved in bringing a new product to the market. This information aids in pricing strategies, ensuring profitability, and identifying potential cost-saving opportunities throughout the product development process.
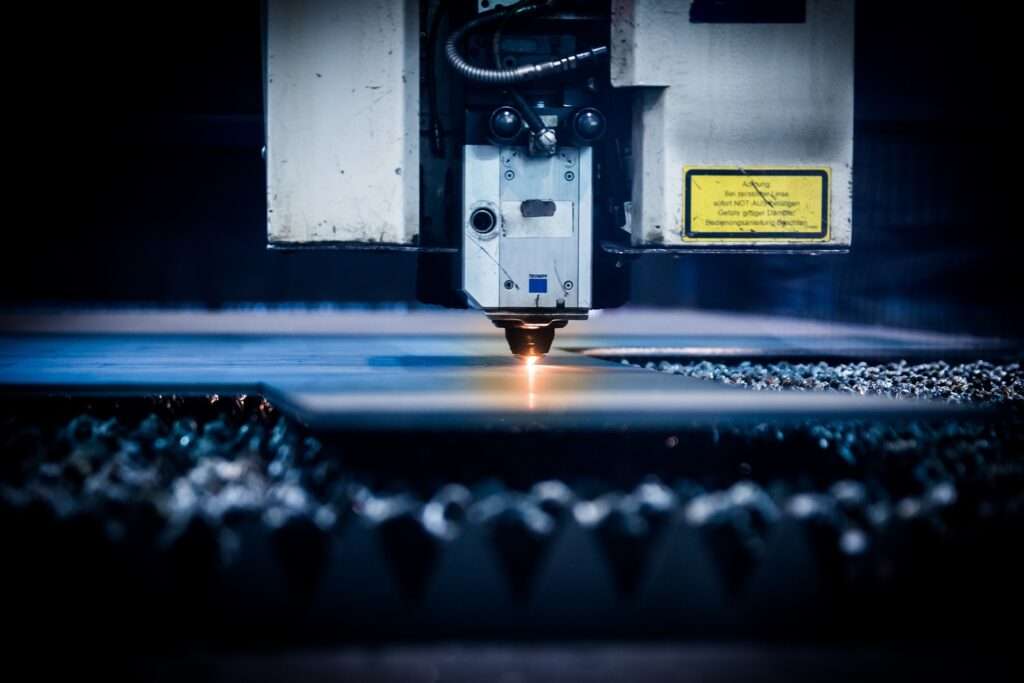
XIII. Transitioning to Activity-Based Costing
Transitioning from traditional costing methods to Activity-Based Costing requires careful planning and execution. Here are the steps involved in the transition process:
1. Assess the organization's current costing system
Before transitioning, it is essential to evaluate the strengths and weaknesses of the organization’s current costing system. This assessment will help identify areas for improvement and provide a starting point for implementing ABC.
2. Educate and train employees
To ensure a smooth transition, it is crucial to educate and train employees on the principles and benefits of Activity-Based Costing. This will help them understand the purpose and significance of the change and support its successful implementation.
3. Gradual implementation and testing
Rather than a sudden shift, it is often advisable to implement ABC gradually, focusing on one department or product line at a time. This approach allows for testing and fine-tuning of the ABC system before full implementation.
4. Continuous monitoring and refinement
Transitioning to ABC is an ongoing process that requires continuous monitoring and refinement. Regular review and analysis of the ABC results will help identify any issues, make necessary adjustments, and ensure the accuracy and relevance of the system.
XIV. Benchmarking Activity-Based Costing
Benchmarking ABC involves assessing the effectiveness of ABC in organizations and comparing the results across different industries. This analysis allows organizations to identify best practices, determine areas for improvement, and set realistic goals for their ABC system. By benchmarking ABC, organizations can optimize their cost management strategies and stay ahead in an ever-evolving business landscape.
XV. Success Factors for Activity-Based Costing
The successful implementation and utilization of Activity-Based Costing depend on several key factors:
1. Executive support and commitment
The support and commitment of top-level executives are critical for the successful adoption of ABC. Leaders must champion the initiative, allocate necessary resources, and communicate the importance of ABC to all employees.
2. Employee involvement
Involving employees at all levels in the ABC implementation process is vital. Their active participation and feedback can help identify potential cost drivers and activities, ensuring the accuracy and relevance of the ABC system.
3. Continuous improvement mindset
A continuous improvement mindset is essential for maintaining the accuracy and effectiveness of ABC. Organizations must foster a culture of learning, encourage feedback, and promote a willingness to adapt and refine the ABC system as needed.
XVI. Future Trends and Innovations in Activity-Based Costing
As technology advances at an exponential rate, the future of ABC is likely to witness exciting innovations. Automation, artificial intelligence, and machine learning are expected to revolutionize the way ABC data is collected, analyzed, and utilized. These advancements will further enhance accuracy, efficiency, and the ability to derive valuable insights from ABC systems.
XVII. Summary
Activity-Based Costing (ABC) is a powerful cost management strategy that helps organizations gain a comprehensive understanding of their costs. By tracing costs back to specific activities, ABC provides a more accurate picture of product and service profitability. Implementing ABC requires careful planning, accurate identification of cost drivers, and allocation of costs based on resource consumption. Industries such as manufacturing, service, and healthcare have witnessed significant benefits from ABC implementation. Despite its challenges, ABC improves decision-making, enhances resource allocation, and aids in performance measurement.
XVIII. FAQs about Activity-Based Costing
Q1. What are the key differences between traditional costing methods and Activity-Based Costing (ABC)?
- Traditional costing methods rely on broad and arbitrary allocations of overhead costs, while ABC traces costs back to specific activities.
- Traditional costing often fails to accurately allocate indirect costs, resulting in distorted cost information, whereas ABC offers a more accurate distribution of costs.
- ABC provides a more detailed and granular view of cost allocation compared to traditional costing methods.
Q2. Is Activity-Based Costing suitable for all industries?
Activity-Based Costing can be applied to various industries. While it is particularly effective in manufacturing, the service industry, and healthcare organizations, any industry that seeks to gain a detailed understanding of their cost structure and improve decision-making can benefit from ABC.
Q3. Is implementing Activity-Based Costing time-consuming?
Implementing ABC can be a time-consuming process, especially during the initial stages of identifying cost drivers and activities. However, the benefits gained from the accurate cost allocation and improved decision-making make it a worthwhile endeavor.
Q4. Can technology integration enhance Activity-Based Costing?
Yes, integrating technology and automation into the ABC process can streamline data collection, analysis, and reporting. Specialized software solutions designed for ABC can reduce manual effort and enhance accuracy, efficiency, and effectiveness.
Q5. How does Activity-Based Costing contribute to resource allocation optimization?
Activity-Based Costing links resource consumption to costs, allowing organizations to identify activities with high resource demand. By allocating their resources efficiently based on ABC data, organizations can optimize resource allocation, maximize profitability, and eliminate wasteful spending.
Q6. Can Activity-Based Costing be used as a performance measurement tool?
Yes, Activity-Based Costing can be utilized as a performance measurement tool. By analyzing key performance indicators derived from ABC data, organizations can evaluate the efficiency and productivity of various activities, departments, or products. This analysis informs decision-making, identifies areas for improvement, and helps organizations enhance overall performance.